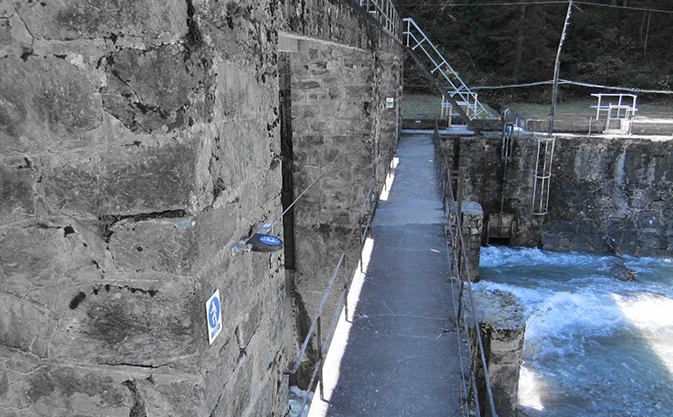
La instalación de los anclajes estructurales
La seguridad y salud del trabajador que lleve a cabo un trabajo de acceso mediante cuerdas o en alturas, es clave la correcta instalación de un sistema de anclaje, ya sea por medio de una instalación de cuerdas o a la hora de llevar a cabo la instalación de una cinta de anclaje. Pero no nos podemos olvidar de lo más importante, que es la correcta instalación del anclaje estructural.
Tener un conocimiento de los elementos estructurales que servirán de apoyo a los puntos de anclaje y saber como va a ser su rendimiento en cuanto a fijación, así como, de la correcta elección de los anclajes para el tipo de material que servirá de base, es esencial para llevar a cabo un trabajo seguro, sin riesgo de que se produzca un arrancamiento del anclaje.
DEFINICIONES:
Antes de entrar a fondo en las instalaciones es conveniente tener unos criterios claros para saber a qué nos referimos en cada caso a la hora de llevar a cabo las explicaciones. Saber diferenciar los conceptos es muy importante para no llevar a confusiones y tener las ideas los más claras posibles:
• DISTANCIA ENTRE ANCLAJES ESTRUCTURALES: Es aquella distancia mínima existente que debe respetarse entre los ejes de los anclajes instalados en un mismo soporte.
• DISTANCIA CORRECTA ENTRE ANCLAJES ESTRUCTURALES: Es toda distancia entre los ejes de los anclajes que comparten un soporte y cuyo rendimiento es óptimo, al generar el mayor soporte de carga posible.
• DISTANCIA MÍNIMA AL BORDE: Es toda distancia mínima que debe respetarse entre los ejes den anclaje y al borde del hormigón más cercano.
• DISTANCIA IDEAL AL BORDE: Es aquel a la distancia entre el eje del anclaje y el borde de hormigón en donde la carga aporta su mayor rendimiento.
• ESPESOR MINIMO DEL SOPORTE: Es el espesor mínimo que debe tener el soporte donde se va a instalar el anclaje.
• PROFUNDIDAD EFECTIVA DEL ANCLAJE: Es la longitud del cuerpo del parabol que se introduce en el orificio y que será la parte que absorbe la carga que se genera.
• DIÁMETRO DE LA BROCA: Es el N.o de diámetro de la broca indicado para realizar el orificio en relación al diámetro del parabol.
• PROFUNDIDAD MINIMA DE TALADRO: Es la profundidad de taladro necesario a realizar en el soporte mínimo.
• DIÁMETRO DE TALADRO PIEZA A FIJAR: Es el diámetro de taladro en la pieza que va a actuar de soporte.
• PAR DE APRIETE: Indica la fuerza de apriete a aplicar en el anclaje. Para ello debemos ayudarnos y usar una llave dinamométrica que fija la fuerza necesaria para que el anclaje actúe plenamente.
TIPOS DE INSTALACIÓN DE LOS ANCLAJES ESTRUCTURALES

Podemos diferenciar dos tipos de instalaciones, conforme al número de anclajes que se van a realizar en relación a las capacidades de carga a soporta y si se quiere hacer una distribución de los mismos.
• La instalación simple:
· El montaje solo tiene un anclaje estructural.
· No depende de ninguna separación respecto a otros anclajes.
· Sí que es muy importante saber que cono de rotura se puede generar para que se produzca una distribución de carga equitativa en todo el bloque. Por lo tanto, no podrá realizarse cerca de los extremos o bordes.
• La instalación múltiple:
· El montaje se compone de varios anclajes estructurales.
· El fin de esta es la distribución y un reparto de las cargas de manera uniforme entre los mismos y por lo tanto aumentar la eficacia de carga.
· Es muy importante no solo tener en cuenta la instalación respecto al borde, sino también respecto a los otros anclajes debido a que los conos de rotura que se generen por su instalación no pueden ser invadidos entre ellos, solapándose, debido a que provoca una debilitación de la zona o estructura donde se hayan instalado.
A TENER EN CUENTA EN LA INSTALACIÓN DE LOS ANCLAJES ESTRUCTURALES
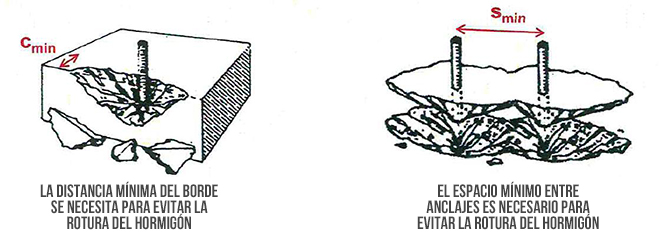
Los factores a tener en cuenta antes de empezar la instalación son:
• En la base a instalar: Resistencia, tipo de base, dimensiones de la base (profundidad, anchura longitud...) grosor de la pieza...
• En el anclaje: Instrucción DITE, selección del mismo, certificaciones y espesor máximo de la pieza, diámetro del taladro, distancias entre taladros...
ERRORES EN LA INSTALACIÓN DE LOS ANCLAJES ESTRUCTURALES
Durante las instalaciones, ya sea por la rapidez al llevar a cabo la instalación, las prisas, la económica o meramente un tema de no dar importancia a la acción de llevar a cabo el anclaje, puede conducir a que se produzcan varios errores durante el proceso:
• Taladros realizados incorrectamente:
· Agujeros mal ubicados.
· Agujeros poco profundos.
· Agujeros que choquen con las varillas que conforman el encofrado.
· Roturas externas que provoque el taladro.
· Grietas en las armaduras del hormigón.
• No usar la llave dinamométrica:
· Falta de par de apriete y por lo tanto la expansión del anclaje mecánico no completa.
· Demasiado par de apriete, que provoca una sobrecarga en el anclaje provocando demasiada tensión en las paredes del agujero dañando la estructura del orificio y disminuyendo la capacidad de carga.
• Tiempo de secado del anclaje químico:
· Tipo de resina y composición, afectando al endurecimiento.
· Temperatura del material base y condición atmosférica. Siempre debe respetarse el periodo de secado entre la colocación y uso del anclaje. El fabricante marca los tiempos según las condiciones, y no depende tanto de la acción del instalador, sino de su paciencia.
• Distribución incorrecta de las cargas:
· No respetar la distancia mínima al borde del bloque.
· No respetar la distancia entre los ejes de los anclajes.
FALLOS QUE SE PUEDEN PRODUCIR EN LOS ANCLAJES MAL INSTALADOS
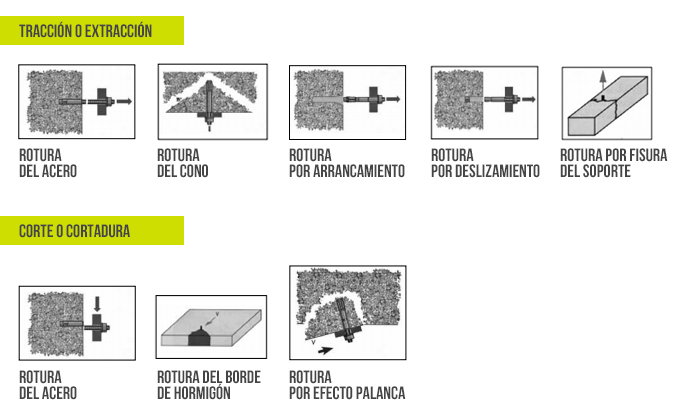
Como hemos comentado, las cargas se generan tanto a tracción o extracción y a corte o rayadura. Si entramos mas profundamente podemos definirlas como:
• A extracción: es cuando la carga que se genera tirando del anclaje en la dirección contraria a la que se ha ido instalando.
• A cortadura: es cuando la carga que se genera es en el sentido contrario a la dirección que ha sido colocado el anclaje, pero hacia arriba o hacia abajo.
TIPOS DE ROTURA QUE PUEDEN PRODUCIR UNA MALA INSTALACIÓN
Tipos de rotura que puede generar una mala instalación conforme a la fuerza generada:
• TRACCIÓN O EXTRACCION:
o Rotura del acero: se produce cuando el ejerce del parabol se parte provocado por una gran profundidad de la inserción en un hormigón de alta resistencia.
o Rotura del cono: las fuerzas de tracción se aplican en una zona del hormigón que sea de baja resistencia o mala distribución de la carga.
o Rotura del arrancamiento: el anclaje no genera en el interior del orificio la expansión ni tensión necesaria. Puede ser provocada por usar una métrica de taladro superior a la debida.
o Rotura por deslizamiento: al superar la resistencia en la expansión, el perno puede deslizarse a través del casquillo de expansión permaneciendo este en el interior.
o Rotura por fisura del soporte: las dimensiones del soporte no son suficientemente requeridas y provoca la fisura de este.
• CORTE O CORTADURA:
o Rotura de acero: el anclaje no esta suficientemente introducido en el orificio o el orificio es menos profundo de lo necesario. El peso genera una carga que parte el perno.
o Rotura del bode de hormigón: el anclaje se instala cerca del borde o esquina y la carga se genera en la dirección del borde.
o Rotura por efecto palanca: no se ha realizado una profundidad necesaria en el taladro y eso genera que se arranque el paramento.
LOS ANCLAJES ESTRUCTURADOS EN LAS LINEAS DE VIDA
Los anclajes para las líneas de vida, están regulados por la norma UNE EN 795:2012, que recogen los equipos de protección anticaídas, concretamente los dispositivos de anclaje.
Los requerimientos recogidos para los anclajes fijos o EN 795:2012 clase “A” son los siguientes:
• Debe de comprobarse la deformación por medio de la realización de un ensayo estático con carga de 0.7-0.8 kN durante 1-1.25 minutos. Debe comprobarse si la deformación permanente es mayor de 10 mm.
• En ensayo estático, el anclaje debe resistir una carga de 12-13 kN en la dirección de trabajo durante al menos 3-3.25 minutos.
• En ensayo dinámico, la carga de 1 kN liberada desde una altura de 2 metros, antes de que el elemento de retención empiece a actuar, generando una carga de retención de la caída de 9-9.5 kN.
Es recomendable que una vez fijado, llevar a cabo una realización de la capacidad portante aplicando una fuerza axial de 5 kN durante al menos 15 minutos.
Los distintos dispositivos deberán de usarse con antiácidas con marcado CE que no generen nunca fuerzas superiores a 6 kN, es decir, un absorbedor de energía que recoja la fuerza del golpe.